Use of modern technology in onshore farming
Land-based Recirculating Aquaculture Systems (RAS) are an advanced, typically environmentally benign technology used to grow safe and healthy seafood in large tanks. Utilizing RAS for land-based farming of aquatic animals has notable advantages over the traditional marine and other net-pen aquaculture operations. Unlike offshore farms, RAS provides Aquabanq with near-total control over growing conditions and inputs. This technology allows us to optimize growth, prevent diseases, and ensure quality, in order to supply shrimp according to a predictable year-round production plan.
The excessive use of antibiotics in traditional aquaculture and livestock farming has transformed what had been a hypothetical menace into a real public health emergency: the rise of antibiotic-resistant bacteria, which are alarmingly impervious to treatments. Eliminating entry points for pathogens and parasites as well as providing overall good health conditions for our fish and shrimp in a tightly controlled RAS environment ensures that no antibiotics are used, be discharged with effluent, or enter the food chain through the consumption of our product.
The water in our RAS is reused and continuously treated. The system decreases dissolved carbon dioxide and nitrogen gas to levels closer to atmospheric saturation, and increases dissolved oxygen concentrations above atmospheric saturation levels. Additional treatment units disinfect and oxidize organic wastes and nitrite in order to supplement the effectiveness of other water treatment units.

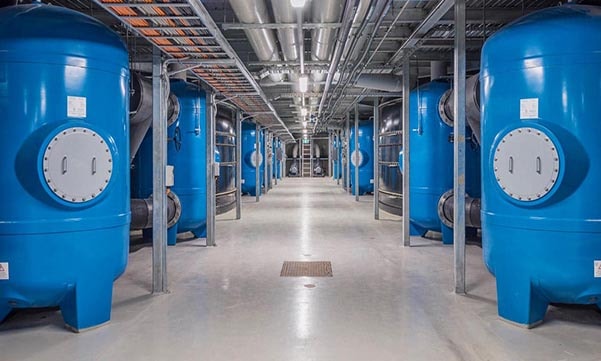
ZERO-DISCHSARGE RAS
Our standard zero-discharge RAS unit is designed to produce 275 thousand pounds* of shrimp annually at a harvest size of eighteen to twenty-two head-on shrimp per pound, operating at 65% of system capacity. The production can be scaled up within just a few months as Zero-Discharge RAS discharges no liquid effluent or to surface waters or the ground.
The system recirculates process water through two separate treatment loops using anaerobic and aerobic filtering process. Subsequently, the purified and oxygenated water flows back into the production tanks.
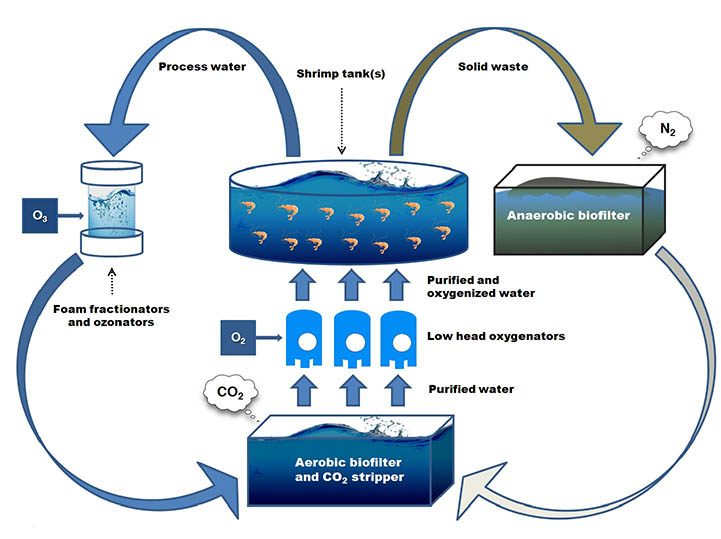
For many years, all land-based aquaculture systems used mechanical, microscreen drum filters to remove solid waste such as fish feces and uneaten feed. The sludge was then collected in tanks and transported off-site to a nearby treatment facility. The process inside the anaerobic tank in zero-discharge RAS utilizes anaerobic bacteria to break down ammonia and proteins.
